When it comes to selecting a welding screen, safety is the top priority. These screens serve as a protective barrier against harmful radiation, sparks, and welding splatter. However, you might wonder whether the color of your welding screen matters. This blog will explore the significance of welding screen colors and help you decide which color best suits your welding needs.
THE PURPOSE OF WELDING SCREEN COLORS
Welding screens come in various colors, each with a specific purpose and set of advantages. The color of your welding screen can influence factors such as visibility, comfort, and the overall welding environment. Here are some standard welding screen colors and their purposes:
1. Green Welding Screens:
Advantages: Green screens provide excellent visibility while blocking harmful UV and infrared rays. They are suitable for most welding applications and offer a balanced environment.
Best For: Green screens are versatile and can be used for oxy-fuel and electric arc welding.
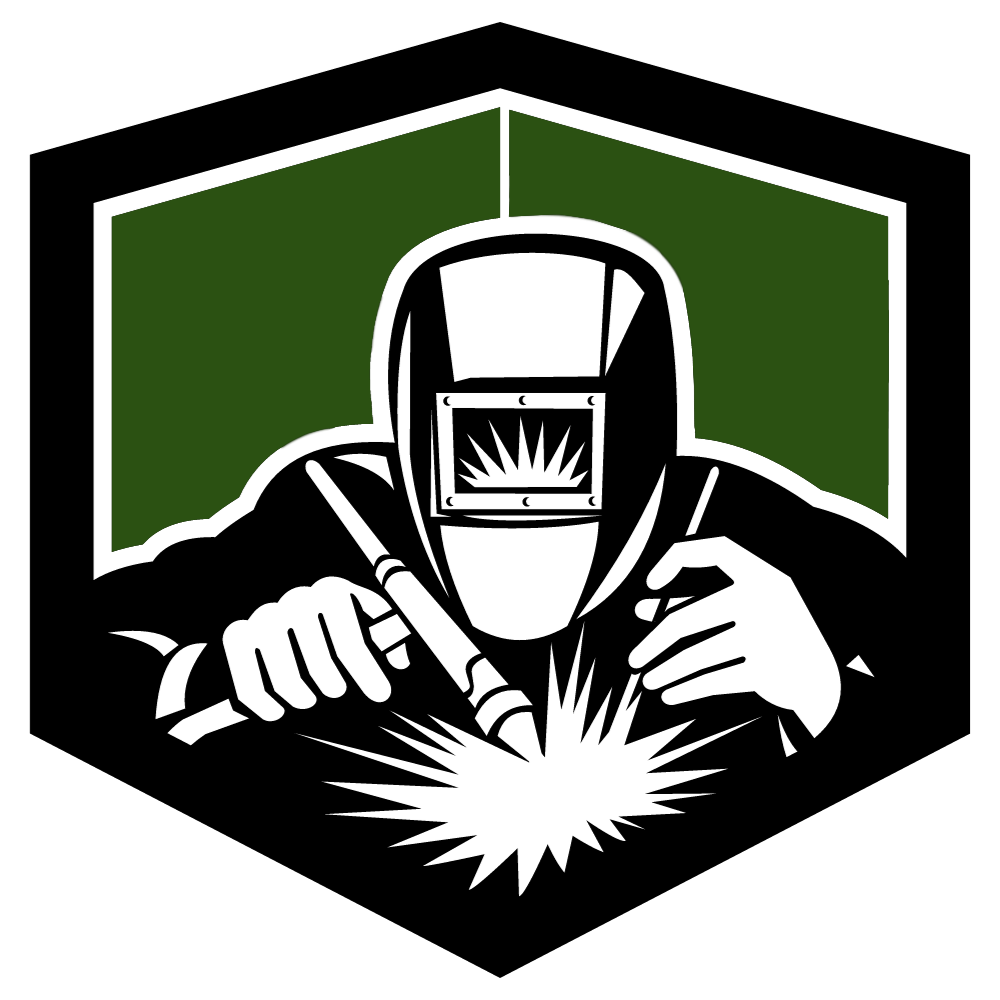
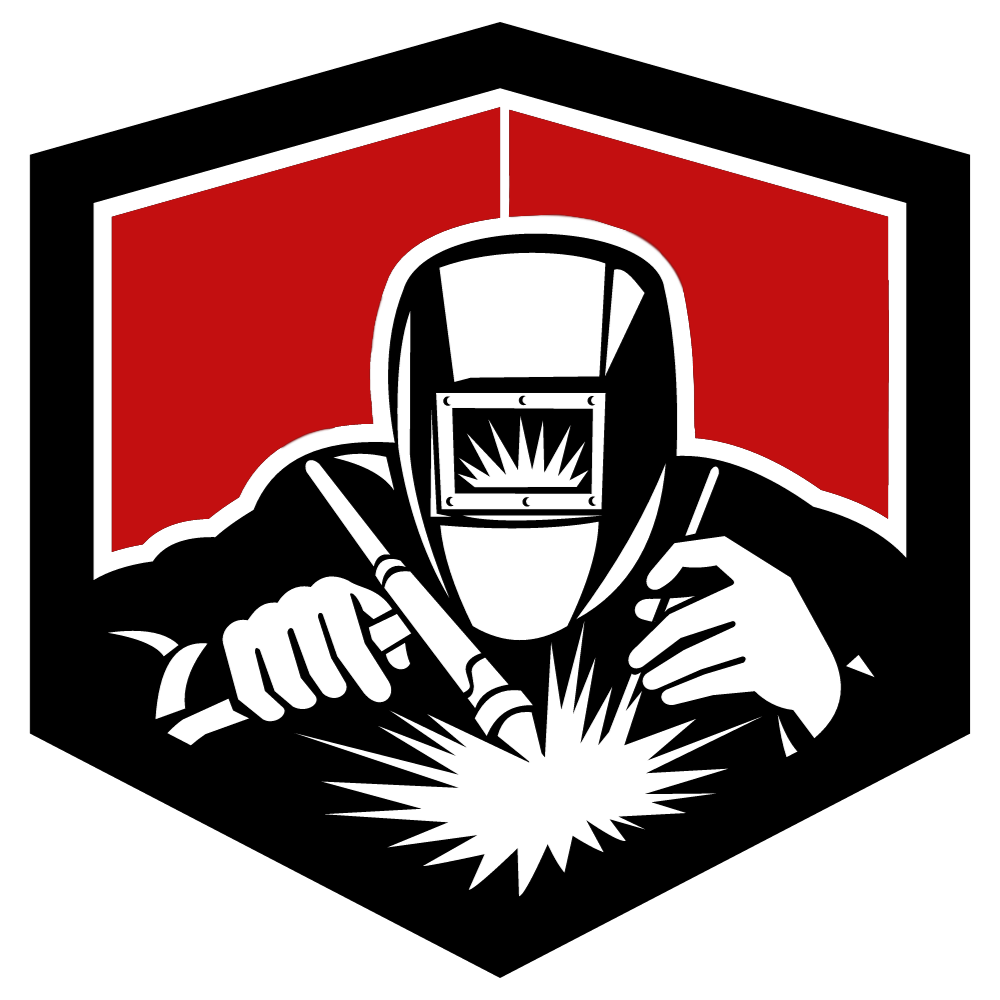
2. Red Welding Screens:
Advantages: Red screens are known for their enhanced visibility and reduced glare, making them ideal for applications where precision and accuracy are crucial.
Best For: Red screens are often preferred for TIG (Tungsten Inert Gas) welding, where welders need a clear view of the welding process.
3. Yellow Welding Screens:
Advantages: Yellow screens offer good visibility and contrast. They are excellent for reducing eye strain and maintaining a comfortable workspace.
Best For: Yellow screens suit general welding tasks, providing a bright and well-lit environment.
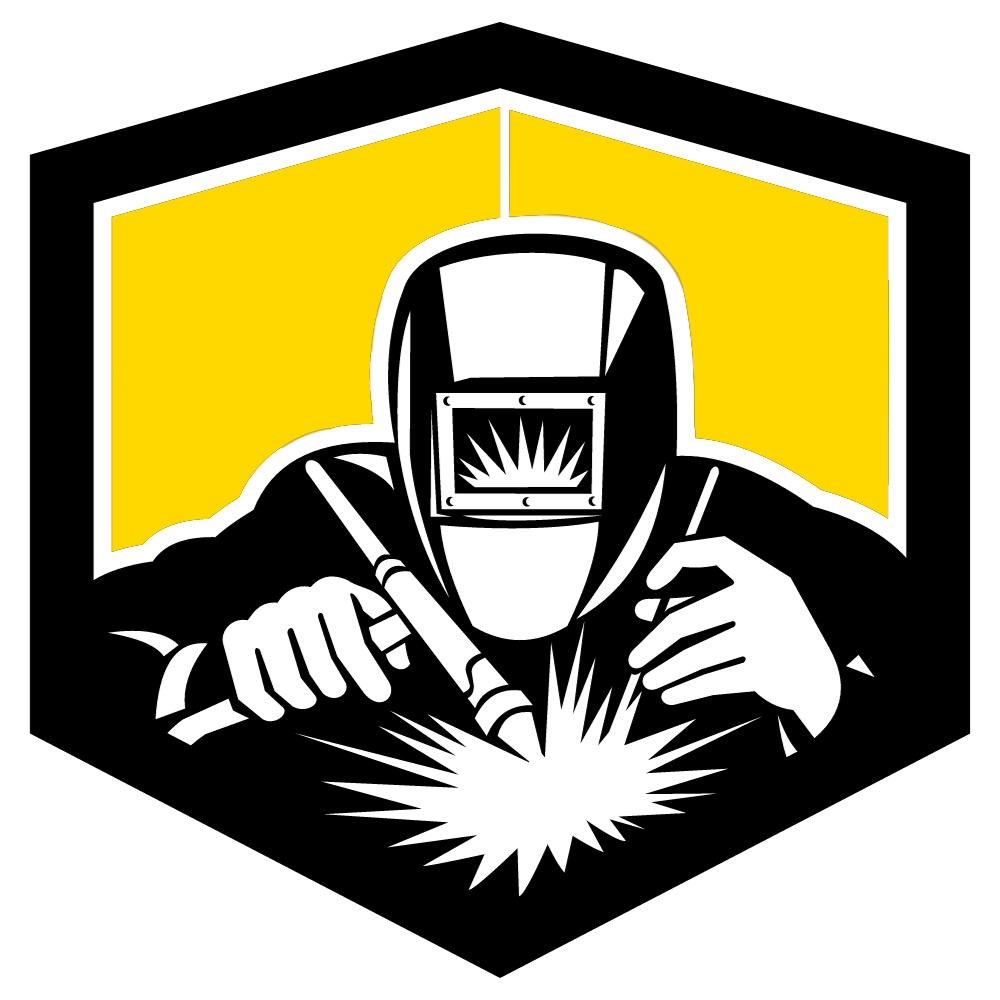
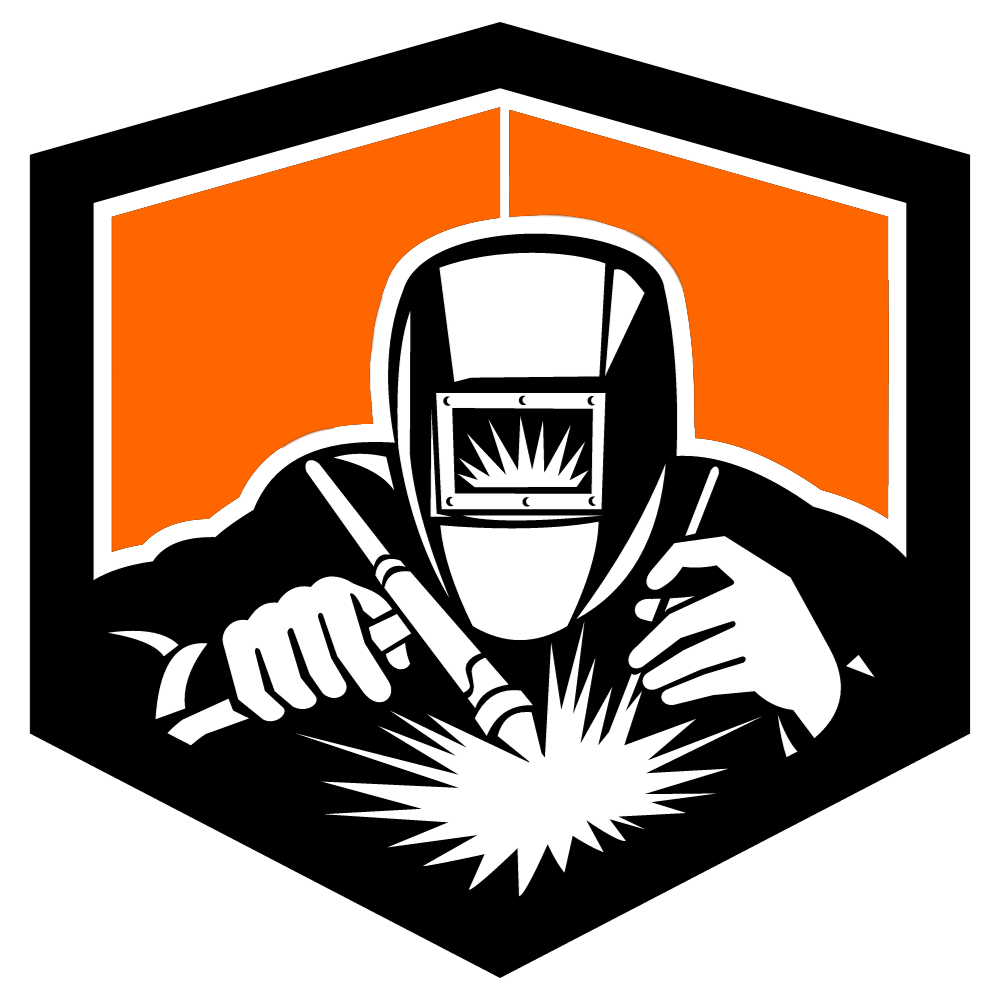
4. Orange Welding Screens:
Advantages: Orange screens provide a balance between visibility and protection. They are known for reducing fatigue and maintaining alertness.
Best For: Orange screens are often used in areas where welders need to stay focused for extended periods.
5. Blue Welding Screens:
Advantages: Blue screens are designed to reduce glare and increase visual comfort. They are suitable for tasks where workers must concentrate on their work for extended periods.
Best For: Blue screens are commonly used in industries like shipbuilding and aerospace.
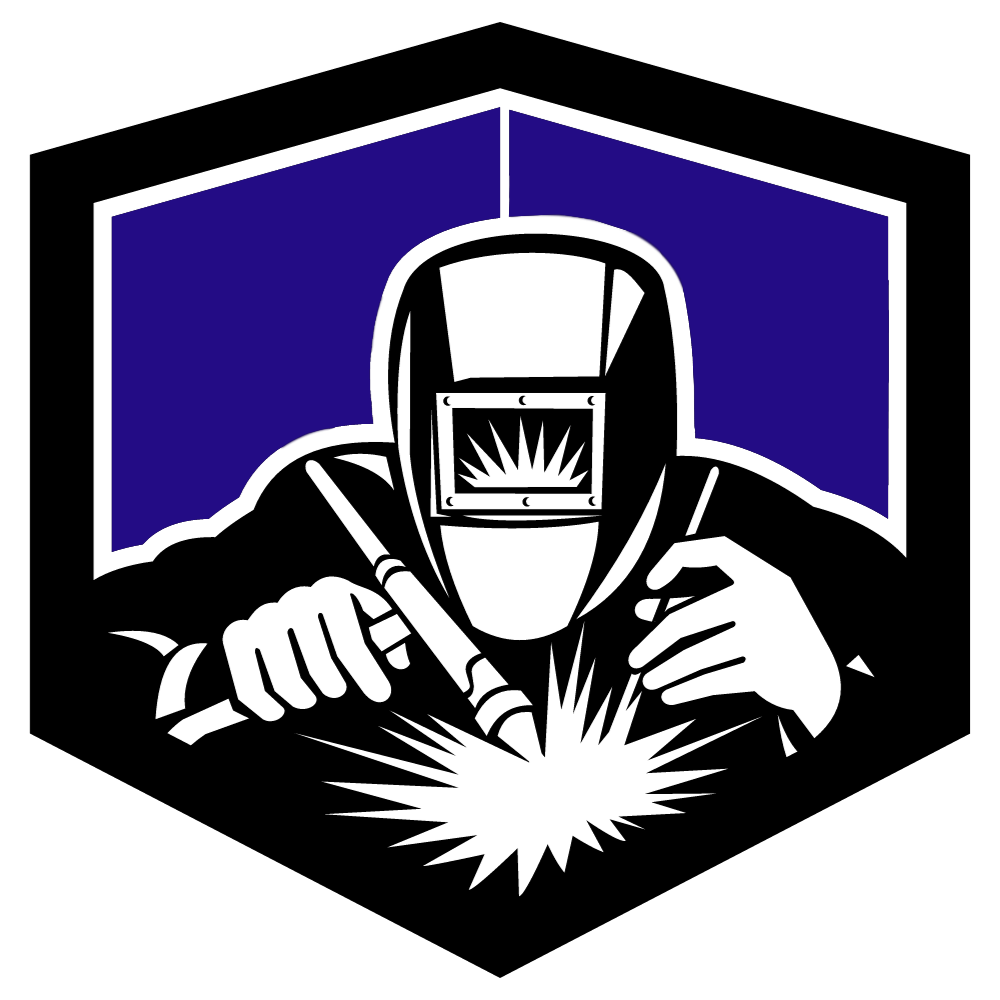
CHOOSING THE RIGHT COLOR FOR YOUR WELDING SCREEN
Now that you have an understanding of the different welding screen colors and their purposes consider the following factors when selecting the right color for your welding screen:
1. Type of Welding: Your specific welding process plays a significant role. For instance, TIG welders may prefer red or green screens for precision, while MIG or stick welders may find yellow or orange screens more comfortable.
2. Personal Preference: Your personal comfort and visual preferences matter. Some welders find specific colors more visually appealing and less fatiguing.
3. Work Environment: Assess your work environment. If you’re working indoors with controlled lighting, you may have more color flexibility. However, the color choice becomes more critical for outdoor welding or areas with variable lighting conditions.
4. Safety Regulations: Some workplaces have safety regulations that specify the color of welding screens. Always adhere to these regulations to ensure compliance.
CONCLUSION
The color of your welding screen can significantly impact your welding experience. While safety remains paramount, the choice of color can enhance visibility, reduce eye strain, and create a more comfortable working environment. Consider your specific welding tasks, personal preferences, and workplace conditions when selecting the color of your welding screen. Ultimately, the right color choice will help you work more efficiently and safely in the welding environment, ensuring a smoother and more enjoyable welding experience overall.